产品的安全与可靠性是人们经常提及的话题,前者往往涉及产品与人的关系,后者令人联想到产品的质量。随着社会经济水平的发展,科技的进步,在产品的功能与质量不断完善中,机械产品是否安全与可靠,是社会愈来愈关注的问题,尤其是产品对消费者的安全性。纵观世界市场,发达的西方工业国家在运用了可靠性技术提升了产品质量的今天,又将产品是否满足安全与卫生的基本要求提到议事日程上来。安全性既是构建和谐社会的重要因素,同时又是发达国家为保护其国内产品而设立技术性贸易壁垒的主要“借口”之一。
最早的可靠性研究源于XXX,借助于二次世界大战,可靠性工程及研究得以发展。此后,可靠性工程在航空、航天以及日常工业领域中均取得了巨大进展,到上世纪七十年代后期,美军的可靠性标准体系已基本完整建立。1985年,由德国著名工业安全科学学者库赫曼(kuhlmann)所著的世界上第一本《安全科学导论》在欧洲发行,标志着安全科学作为一门独立的学科,在人类科学技术大家庭中成为独立成员。我国于1992年,将安全科学技术作为一个独立的一级学科,在国家标准GB/T13745-92《学科分类与代码》中予以规定,可靠性则以数学、航天航空以及计算机学科之下的二或三级学科而出现。
机械的安全性与产品的可靠性,其内在联系与区别及关系是本文将主要探讨的题目。
1.问题的两个侧面
提起产品,人们首先想到的就是质量。在市场经济的时代,质量可以说是市场竞争的资本,而市场的占有率又直接关系到生产厂家的生存大计。
质量(quality)是反映实体满足规定和潜在需要能力的特性的总和。这里潜在需要是指,用户在合同或定单中未明确提出但实质上有的需要。82版的国标3187(可靠性术语)中,曾经给出一个框图(见图1),产品的总能力可分为安全性与效能两个主要部分。效能是指产品的技术性能、操作性能和产品的广义可靠性。安全性能则与人员的操作能力、产品的耐久性、可靠性以及维修支援性或后勤保障性相关。这个框图表达了在产品质量中,安全性与可靠性的一个关系(尽管92版的GB3187不再提及其)。
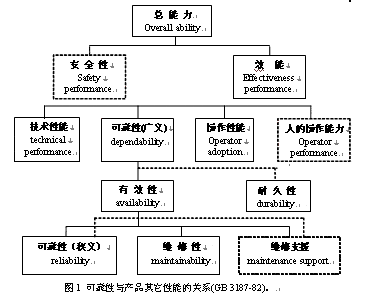
由此可见,作为实体的一项重要特性,质量应包括产品的:
•性能(performance)
•适用性或易用性(usability)-- 便于用户使用的能力
•可信性(dependability) –包括可靠性、维修性、维修保障性等与时间有关的量
•安全性(safety) -- 将伤害或损坏的风险限制在可接受的水平
•环境(environment) – 对环境的影响,有时也是安全性能的一个组成部分
•经济性(economic)
•美学(aesthetics)
一旦产品的性能确定了,如何保证在规定的时间内,产品能够达到规定的功能这就是可靠性要解决的问题,产品的寿命问题。产品的功能需要人去控制、使用、维护时,产品与人之间的关系,产品对人的安全性又成为社会关注的重点。安全性理所当然地成了产品的总能力的重要部分。
作为国民经济主力军的制造业,工作母机的安全与可靠性应受到机械行业的重点关注。安全从来都是伴随生产而行的。不安全的机器,寿命越高,可能会带来越多的伤害,导致社会的不安定;反之不能生产出可靠的产品的机器,即便安全,也是没用的东西,它不能创造价值。安全与可靠性是产品能力的两个重要侧面,它们之间,既有联系,又不可完全取代对方。如同车之两轮、鸟之双翼,相辅相成、缺一不可。
2.机械的本质安全
本质安全来源于英文inherently safe,即固有安全的意思。机械达到了本质安全,就是说机械本身对于与其接触的人不存在危险,是安全的。这实际是机器的设计者为之努力的方向,也是制造商应达到的目标。为此首先应明确影响机械本质安全相关的要素
2.1安全要素
从安全科学的角度出发,安全是指人、物以及人与物之间的和谐并存关系。人、物以及人与物的关系为安全的三要素。在特定的理想状态下,人、物或人与物的关系的任一要素自身即能够独立地成为实现安全的充分条件。
- 人若能对危害因素具有绝对的抵御能力;或
- 物(如设备、物质环境)绝对无危害;或
- 人与物的关系能够在时空和能量、信息上与人绝对不发生危险性联系,
三者若具其一,其结果都是安全的。人、物以及人与物的关系是安全的要素。且三要素和谐并存及其有机联系,将构成现实中的各种安全系统。
在机械工程中,人即为机械的操作使用人员和机器的设计人员,物即为人使用的和设计的机器,人与物的关系一方面表现为:人适应机器的要求,即遵守机器运行的规律,遵守生产活动的规律。这实际是人们常说安全生产与劳动保护;另一方面又表现为对安全生产与劳动保护措施的监管。如果说,我们以往在“人”和“人与物”方面做了很大努力的话,那么进一步提升机器的安全性能已经成为保证安全生产的迫切要求。从机器需要人进行设计这个关键点出发,解决安全问题。
西方国家,尤其是工业发达国家更推崇“机器的自身安全”。再好的机器操作人员,也不能保证一直适应机器的要求;再好的管理,也不能避免人员的失误。一个好的设计会使“物”——机器,从本质上更加安全。从“物”的安全的角度出发,消灭或减少机器的危险将会达到事半功倍的效果。这也是经济发展到一定程度的结果。
2.2机械设备的本质安全
机械设备的本质安全,是指设备系统本身所具有的、固有的、根本的品质特性,真正达到使人不受机器危害的实质性内容。它包括设备的结构、类型、材料、工艺、控制、防护、救助功能以及人与机械设备、人—机—环境在安全方面的总体协调和匹配关系、效能及其质量。
一般地说,机械设备安全本质化的基本内容包括:较完善的安全设计;较完善的安全工效学设计;足够的可靠性和安全质量。在这里,安全工效学或人类工效学,尽管它是一门学科,但其是安全设计中解决机器适应人的重要原则。
较完善的安全设计包括对材料的安全选择和使用,使机械设备的结构本身具有较完善的安全防护和安全保护功能三方面内容。
(1)对材料的选择不但要满足其功能的要求,而且要同时满足使用过程中的安全、卫生要求。此外,还要考虑使用环境的影响和超负荷工作的可能性而留有足够的安全储备。
(2)在安全防护设计上,设计应考虑机械设备的危险部件对作业人员的安全防护设计和防止异物或环境要素作用而导致机器设备故障、失灵的设备自身防护设计。
(3)安全保护设计,即为保证机械设备在寿命期内安全、正常地运行的安全控制设计,涉及机械设备的故障保护,超载,超限、超位及人员误操作保护等诸方面,是机械安全工程的重要研究内容。
较完善的安全工效学设计。正确地设计人机界面,是减少操作失误、提高工效的重要方法。尽可能从人的安全、舒适地工作和运用需要出发,合理设计机械设备有关安全控制部分和操作环境,包括照明、温度、振动、噪声、粉尘和毒物、污物排放等安全卫生问题的处理手段和技术措施。
足够的可靠性和安全质量。机械设备的加工、装配、制造、检修和维护必须可靠,必须保证其在寿命期内按设计的运行速度、工作负荷及环境条件下使用不发生意外故障、损坏或失灵。机械设备的安全质量应主要通过设计、加工、制造、装配及维修质量控制予以保证。
2.3机械安全设计
安全设计的总体目标是使机械产品在其整个寿命期内都应是充分安全的。即在设计时就应对其制造、运输、安装、调试、设定、示教、编程、过程转换、运行、清理、查找故障、维修以及从安全的角度停止使用、拆卸及处理的各个阶段进行研究,并针对上述各阶段(除制造外)编制安全操作说明书。为确保机械安全,需从设计(制造)和使用两方面采取安全措施。凡是能由设计解决的安全措施,决不能留给用户去解决。当设计确实无力解决时,可通过使用信息的方式将遗留风险告诉用户,由用户使用时采取相应的补救安全措施。要考虑合理可预见的各种误用的安全性。采取的各种安全措施不能妨碍机器执行其正常使用功能。
2.3.1 机械安全标准的产生
鉴于欧共体各国早在上世纪80年代就机械安全的立法与标准建立已经开始了的工作。国际标准化组织(ISO)认为,在机械安全方面有必要与欧洲标准化委员会(CEN)加强联系与合作,以尽快消除国际范围内可能产生的机械产品贸易技术壁垒。为此ISO与CEN先后签订了“技术信息交换协议”(里斯本协议)和“技术合作协议”(维也纳协议)。1991年l月,ISO成立了“机械安全技术委员会”,编号ISO/TC199。从安全角度对机器的设计从此有了国际标准。
为了解决国内机械安全标准化工作统一归口问题,我国的全国机械安全标准化技术委员会(SAC/TC208)于1994年11月正式成立,它与ISO /TC199直接对口,其工作范围与ISO /TC199和CEN/TC114相同。到目前为止,在ISO/TC199所制定的机械安全标准共计26项,另有标准草案10项中,我国已经转换并发布了标准21项,另有3项待发布。根据我国的具体情况,SAC/208还转换了7个欧洲标准。它们是:《用于机械安全的人类工效学设计》的第1部分:全身进入机械的开口尺寸确定原则、第2部分:人体局部进入机械的开口尺寸确定原则和第3部分:人体测量数据和《机械安全 安全标准的起草与表述规则》;《梯子》的第1部分:术语、型式和功能尺寸、梯子、第2部分:要求、试验和标志。前四个标准从人类工效学的角度规定了机器开口的安全尺寸和可接触的安全的表面温度,后两个标准是《机械安全 进入机器和工业设备的固定设施》的配套标准。
机械安全的标准是指导机械类进行安全设计的指南与原则。GB/T15706.1、.2正是这样两个基础标准。它们给出机械安全设计的基本原则。GB/T16856给出在安全设计中进行风险评价的方法。这三个标准属于A类基础标准,与SAC/TC208的其余B类通用标准共同组成指导制定针对专用机器设计制造的C类标准。
2.3.2 机械安全设计的基本原则
在进行机械安全设计时,有几个基本应遵守的原则。它们是:
1、进行风险评价的准则
在进行安全设计时,首先要对所设计的机器进行全面的风险评价(包括危险分析和风险评定),以便有针对性的采取有效措施消除或减小这些危险和风险。
2、优先采用本质安全措施的准则
- 尽量采用各种有效的先进技术措施,从根本上消除危险的存在;
- 使机器具有自动防止误操作的能力,使其达到不按规定程序操作就不能动作,或者即使动作也不会造成伤害事故;
- 使机器具有完善的自我保护功能,当其某一部分出现故障时,其余部分应能自动脱离该部分,安全的转移到备用部分或停止运行,同时发出警报并且故障在未被排除之前不会蔓延和扩大。
3、符合人类工效学的准则
人机匹配是安全设计的重要问题之一,设计时必须充分考虑人机特性,使机器适合于人的各种操作,以便最大限度地减轻人的体力和脑力消耗及操作时的紧张和恐惧感,从而减少因人的疲劳和差错导致的危险。
4、符合安全卫生要求的准则
机器在整个使用期内不得排放超过规定的各种有害物质,如果不能消除有害物质的排放,必须配备处理有害物质的装置或设施。
2.3.3 消除或减小风险的方法
从设计角度,在机械安全设计中实现风险减小的过程可用图2所示的流程表示,亦称安全设计三步法。
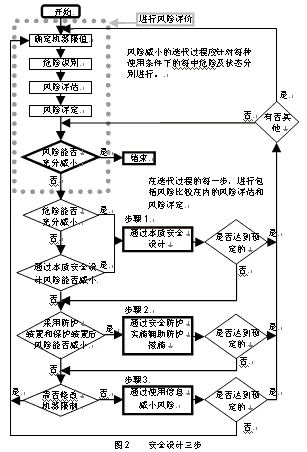
首先对与机械相关的危险进行考察——进行风险评价。风险评价(risk assessment)是包括风险分析(risk analysis)和风险评定(risk evaluation)在内的全过程。这里风险分析主要确定机器限制(机器的功能和指标)、识别(由机器可能产生的)危险和进行风险评估(risk estimation)确定一旦发生伤害后,其可能的产生的严重程度和伤害发生的概率,为风险评定提供所需的信息。风险评定则是基于风险分析,评价、确定机器是否达到风险减小的安全的目的。
风险评定也是一个重要的风险减小的步骤。当结论是通过本质安全设计、通过实施辅助防护措施、继而通过向用户提供风险信息还不能达到减小风险的话,就应该重新进行风险评价活动,或是更改机器的限值等等,直至达到风险减少的目的。
GB/T 15706.1-1995第5章描述了这样的方法,给出可应用的相应的安全措施。重复这一过程,即为可达到尽可能消除危险和根据现有工艺水平实施安全措施的迭代过程。GB/T 15706.1、GB/T 15706.2最新版详细给出进行风险评价和通过设计减小风险的指导步骤。ISO/TC199正在研究将ISO14121《机械安全 风险评价的原则》(即GB/T 16856-1997)分成风险评价第1部分——原理和第2部分实施指南及实例。由此可以看出国际社会在机械安全方面对推行风险评价方法的重视程度。
3.机械产品的可靠性
在产品的全寿命周期中,设计、工艺、制造、试验、维护、售后服务以及相应的管理共同构成产品的质量。可靠性工程技术是以解决产品可靠性为出发点的、综合了众多学科技术成果的边缘科学。它研究的是产品或系统故障发生的原因、故障的消除和预防措施(这一点与安全设计中的风险评价步骤是一致的)。其主要任务是保证产品的可靠性和可用性,延长寿命,降低维修费用,提高产品的使用效益。
从可靠性技术在生产过程中各阶段应用的目的和任务划分,机械产品的可靠性通常又分为:
- 可靠性设计:通过设计奠定产品的可靠性基础,研究在设计阶段如何预测和预防各种可能发生的故障和隐患。
- 可靠性试验:通过试验测定和验证产品的可靠性,研究在有限的样本、时间和试验费用下如何获得合理的评定结果。
- 制造阶段可靠性:通过制造实现产品的可靠性,研究制造的偏差控制,缺陷的处理和早期故障的排除,保证设计目标的实现。
- 使用阶段可靠性:通过使用维持产品的可靠性,研究产品运行中的可靠性监视,诊断预测,采用售后服务和维修策略等防止可靠性劣化。
- 可靠性管理:组织以较少的费用/时间实现产品的可靠性目标,研究可靠性目标的实施计划和数据反馈系统。
可靠性技术是一门多学科综合的边缘科学,并具有反馈和循环的特征。特点之一,管理和技术高度结合。有人把可靠性技术喻为“病疫学”和“病理学”密切结合的技术。病疫学就是分析和追踪故障的起因、产生的环节,然后将信息反馈到有关部门,以指导设计、制造环节的改进,即可靠性管理的任务。病理学则是研究具体故障的消除和预防技术。管理和技术结合,通过管理指导技术的合理应用,这是可靠性技术的基本思想。特定之二,众多学科的综合。产品、系统的可靠性受到多种环节因素的影响。因此,可靠性技术与很多领域的技术密切相关,如系统工程、人机工程、生产工程、材料工程、环境工程、数理统计以及对以往的失效经验进行分析的失效学等,并综合这些领域的技术解决产品的可靠性问题。特点之三,反馈和循环。产品的可靠性首先是设计出来的,然后通过制造达其目标,通过后期的维护保障目标的实现。
3.1可靠性的定义与指标
可靠性(reliability)是指:产品在规定条件下和在规定的时间内完成规定的能力。可靠性的概率度量称可靠度,描述产品可靠性的量称为可靠性参数(reliability parameter)。在可靠性指标的体系中(图3),可以按产品或按材料将参数或指标分类。描述产品可靠性的指标有与寿命相关的耐久性指标,与故障相关的无故障性指标;维修性指标、经济性指标和可用性指标等。如:
– 故障率λ(failure rate),在规定的条件下和规定的时间内,产品的故障总数与寿命单位总数之比。是进行产品可靠度估算的重要参数;
– 平均故障间隔时间MTBF ( Mean Time Between Failure) ,表示产品能够无故障的工作的能力;
– 使用寿命(useful life),产品从交付使用到出现不能接受的故障率(或出现不值得修复的故障)时的寿命单位数。
不同的产品有着不同的可靠性指标。消除故障,延长寿命,降低成本,充分利用是制定产品可靠性指标的原则。
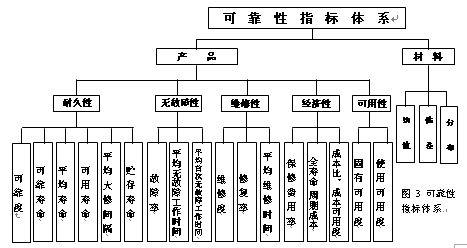
3.2可靠性设计
著名科学家钱学森曾说过,“产品的可靠性是设计出来的,生产出来的,管理出来的”。产品的功能特性在设计阶段被决定下来,其可靠性亦被确定。生产过程和使用过程最多只能保证达到或实现设计的可靠性目标,因此,可靠性设计如同安全设计一样,是保证产品的可靠性的关键步骤。
可靠性设计被定义为:以赋予产品可靠性为目的的设计。它要通过设计,预测和预防产品所有可能发生的故障,使其达到规定的定性或定量的可靠性目标值。
可靠性设计的程序如下:
1)明确可靠性指标 —— 在产品的规划阶段应研究、确定设计的目标值,如整机在功能上应达到的可靠度、平均无故障工作时间等;
2)建立系统可靠性模型 —— 根据系统的各个功能关系,建立其可靠性逻辑关系图及数学公式。可靠性模型是进行可靠性分配、预测和分析的基础。
3)可靠性分配 —— 将系统的可靠性目标值合理地向各构成单元进行分配。如将整机的可靠性指标分配到各个总成,再将总成的指标分配到各零部件,即给出每个单元部件的可靠性指标;
4)可靠性分析 —— 对产品的设计方案进行故障模式影响及危害度分析(FMECA)和故障树分析(FTA)。目的是找出设计上的薄弱点和疏忽,从传统技术和可靠性技术上提出改进措施。
5)可靠性预测 —— 按模型进行可靠性特征值的估算,并与给定的可靠性指标进行比较。若未达到设计的目标值,则进行改进,甚至重新进行可靠性分配;
6)设计评审 —— 在设计方案确定之后,组织专家对方案的各个方面的评议、审查,以发现设计缺陷,提出改进措施,确保设计质量;
7)可靠性试验 —— 在设计方案评审定案后,可试制样机,以便在实际条件下暴露问题,然后进行改进设计。通过设计——试验——再设计的循环获得必要的可靠性增长,达到设计的最终要求。
(根据给定的可靠性目标之进行设计、对已有原型的部分改进设计)
3.3可靠性分析
在可靠性技术中,掌握可靠性的分析方法或分析思路是最重要的。只有找出产品存在的问题,找出问题中的关键问题,解决其,才能有效地提高产品的可靠度。而这个分析的基础方法就是故障模式影响及危害度分析。
3.3.1故障模式影响及危害度影响分析
FMECA是英文Fault/Failure Mode, Effects and Criticality Analysis 的缩写。译为故障模式、影响和危害度分析 (国标GB/T3187-94《可靠性、维修性术语》)。
50年代初,美国Grumman公司第一次将FMEA的思想用于对螺旋桨飞机操作系统向液压机构的改进过程的设计分析,取得很好效果。此后这种方法逐渐被推广,为各国的航天、军工界所采纳,然后推到民用产品,如美国三大汽车公司要求其供货商应具有进行FMEA分析的能力。从标准方面讲,1969年,美军标MIL-S-882(1969年)《系统安全性规范》中采用FMEA和FTA。1979年美国汽车工程师学会出台标准SAE-ARP926《故障和失效分析》。英国标准BS5760《系统、设备和零件的可靠性》(1979)的第三部分中给出FMECA的应用实例。70年代中,美国公布FME(C)A的美军标MIL-STD-1629(后在1980年公布MIL-STD-1629A)。国际电工委员会(IEC)于1985年公布了IEC812,我国等同采用为GB826-87《系统可靠性分析技术 失效模式和效应分析(FMEA)程序》,以及我国军标GJB 1391-92《故障模式、影响及危害性分析程序》。
在FMECA中,故障的表现形式叫“故障模式”(failure/fault mode);故障模式对产品的使用、功能或状态所导致的结果叫“故障影响”(failure effect),一般可分为局部的、高层次的和最终的影响。FMEA研究产品的每个组成部分可能存在的故障模式并确定各个故障模式对产品其它组成部分和产品要求功能的影响,是可靠性的一种定性分析方法。一种故障模式是否值得重视不仅与它的后果有关,而且与它发生的概率有关,对某种故障模式的后果及其出现概率的综合度量叫“危害度”(criticality);同时考虑故障发生的概率与故障危害度的故障模式与影响分析(FMEA)叫故障模式、影响与危害度分析,即FMECA。
引起系统(或装置)整体故障零部件所发生的故障和系统之间存在一定的因果关系。FMECA正是从这种关系出发,通过对系统各部件的每一种可能潜在的故障模式的分析,找出引发故障的原因,确定故障发生后对系统功能、使用性能、人员安全及维修等的影响,并根据影响的严重程度和故障的出现的概率的综合效应,对每种潜在的故障进行分类,找出关键问题所在,提出可能采取的预防和纠正措施(如针对设计、工艺或维修等活动提出相应的改进措施),从而提高系统(或产品)的可靠性。
FMECA方法通常在设计阶段早期进行。目的是使设计人员能够通过一套科学分析的方法,充分了解自己系统中各个组成部分的功能和可能的故障模式,从而在设计工作中有目的的消除或减少潜在的故障。作为产品开发和可靠性设计的重要内容之一,FMECA方法在很多国家中已成为设计分析的基本步骤。
FMECA方法可用于评估设备安全性、修改设计(包括工艺设计)、确定纠正性措施(如维修活动等),亦可用于企业管理。但用在不同的地方就应有不同的侧重。国外一些资料将FMECA分成设计(D-FMECA)、过程(P-FMECA)、分包商及供货商(A-FMECA)及服务(S-FMECA)几大类。
3.3.2故障树分析
FTA是英文Fault Tree Analysis的缩写,称为:故障树分析。故障树分析法由美国贝尔电话研究所的沃森(Watson)和默恩斯(Mearns)于1961年首次提出并应用于分析民兵式导弹发射控制系统的。其后,波音公司的哈斯尔(Hasse)、舒劳德(Schroder)、杰克逊(Jackson)等人研制出故障树分析法计算程序,标志着故障树分析法进入了以波音公司为中心的宇航领域。1974年,美国原子能委员会发表了以麻省理工学院(MIT)拉斯穆森(Rasmussen)为首的有60名专家参与的安全组进行了两年研究而编写的长达3000页的“商用轻水反应堆核电站事故危险性评价”的报告,该报告采用了美国国家航空和管理部于60年代发展起来的事件树(ET: Event Tree)和故障树分析方法,以美国100座核电反应堆为对象对核电站进行了风险评价,使FTA的应用得到很大发展。这一报告的发表引起了各方面的很大反响,被称为FTA发展进程中的一个重要里程碑。并推动了故障树分析法从宇航、核能进入电子、化工和机械等工业领域。
FTA的原理:通过对可能造成产品故障的硬件、软件、环境、人为因素进行分析,从而确定产品的故障原因的各种可能的组合方式和(或)发生概率。可用于复杂系统的功能逻辑分析;分析同时发生的非关键事件对顶事件的综合影响;评价系统可靠性与安全性;确定潜在设计缺陷和危险;评价采用的纠正措施;简化系统故障查找。
FTA可用于系统寿命周期的各个阶段,通常在设计阶段的早期就应进行,以确定设计中固有的潜在故障危险,及时进行设计更改;在设计阶段的后期和批量生产前也应进行,以评价系统是否满足规定的可靠性及安全性要求。
4.安全与可靠性——共通之处
机械安全性是研究如何防止机器风险对人员造成的危害,机械产品的可靠性是解决机器故障对产品质量造成的功能上的危害。研究的对象相同——机器,研究的侧重不尽相同——一个要将机器或其因故障引发的危险限制到最小,一个则是要整体提升机器的质量。显然后者是应当包络前者的。事实上,安全分析的方法与可靠性的分析方法在思路上是共通的,一致的。尤其是设计中对危险或故障的分析上以及反馈循环的设计——改进——再设计过程上,可靠性设计与安全设计是同源的。在设计上,安全设计的步骤是可靠性设计程序中的部分步骤。
表1给出安全设计和可靠性设计及分析过程的比较和对比。可以看出,本质安全设计和固有可靠度设计的性质是一样的。人类工效学或人机工程学设计是二者都要考虑的重要内容。符合安全卫生要求实际上只是安全设计的一个侧重,当考虑与卫生安全相关的机器的可靠性设计时,在规定时间内达到规定的卫生条件可能就是一个可靠性的目标值。可以说,安全设计实际是侧重于安全部分的可靠性设计。
从两种分析方法的对比来看,分析危险或故障的思路是一样的。但与故障(产品不能完成规定功能的状态)相比,危险(导致人员伤亡或设备损坏的实际或潜在的状态)似乎更加“宽泛”。故障模式可以用很简单的词来描述,如断裂。而机械的危险模式,如“挤压危险”,既可以是由机器结构断裂引起的,有可能是由于工件移动引起的,还可能是由于人员的误操作引起的,等等。对待“危险”和“故障”,找出其可能发生的原因、出现后的影响以及防范的措施是两种方法的共同的目的。同时,在设计中,借鉴以往的经验教训,不断地进行风险的评定或危害度的评定,评价——反馈——改进——评价,实际就是可靠性中提倡的“故障报告、分析、纠正措施系统”,又称FRACAS闭环。在设计中发现问题,在解决问题中修改设计,最终拿出一个较为完美的设计。
|
表1 安全性设计与可靠性设计的比较 |
|
安全设计 |
可靠性设计 |
设计法 |
本质安全设计
人类工效学设计
符合安全卫生要求的设计 |
固有可靠度设计
可维修性设计
人机工程学设计
失效安全设计
耐环境设计
冗余、降额设计
…… |
|
风险评价 |
故障模式影响及危害度分析 |
确定 目标值 |
机器的各种限值,如预定使用、运动范围,安装空间及“寿命极限”。 |
机器的可靠性目标值:如达到预定寿命,或首次或平均无故障工作时间。 |
|
风险分析 risk analysis |
|
分解 |
根据机器安全功能框图(GB/T15706.1图1) (未强调) |
根据机器功能框图建立可靠性框图 |
对象 |
机器的危险源:如 机械危险——缠绕、吸入、剪切、…
非机械危险——电、热、辐射、… |
机器可能发生的故障:如 结构故障——开裂、变形、磨损、疲劳、… 功能故障——功能丧失、功能减弱、… |
原因 |
危险产生的原因 |
故障产生的原因 |
|
风险评估 risk estimation |
|
影响程度 |
危险发生后的影响程度 |
故障发生后的影响程度
致命:造成人员死亡,设备严重损坏,经济损失大; 严重:严重损坏,任务不能完成,维修费用高; 一般:停机或性能下降,维修费用一般 轻微: |
频率 |
危险发生的频率 |
故障发生的频率 |
|
其它安全评价参数的确定 |
其它评价用参数的确定(可根据经验) |
|
风险评定——确定机器是否达到风险减小的安全的目的 |
危害度分析——找出影响产品可靠度的关键性故障 |
|
提出对策:按三步法进行检查 |
提出消除或减小故障的措施 |
若未能达到目标,则需反复叠代上述过程。 |
5.结论
本文分别探讨了机械安全设计与机械产品的可靠性设计的内涵、对比了两种分析方法的异同。
- 作为机械产品的效能,其安全性与可靠性是两个重要指标,它们相辅相成,缺一不可;
- 机械的安全性是在其产品的可靠性提高的基础上提出来的,或说,产品的可靠性的进一步提高必然涉及产品的安全性。若要参与国际市场的竞争,必须在提高机械产品的质量——可靠性的基础上(使产品与发达国家之处于同一起跑线),再加以考虑产品是否符合基本的安全与卫生条件;
- 安全的设计理论包含于可靠性设计理论之中,安全的评价方法与可靠性分析方法如出一辙。我们完全可以借用或运用可靠性的理论和方法研究机械的安全问题。
- 机械产品的安全与可靠性不再是超前的要求,达到产品的安全与可靠性已经势在必行。
|